Useful and Proven Tips For Concrete Floor Polishing
There are several things to consider when having your concrete floor polished. These include the sheen level and the dry method. It would help if you also fixed any minor imperfections on the floor before polishing. Finally, it would help if you considered the cost of polished concrete. Using a professional service is well worth the investment. Here are a few tips to ensure your polished concrete is safe for visitors and your family.
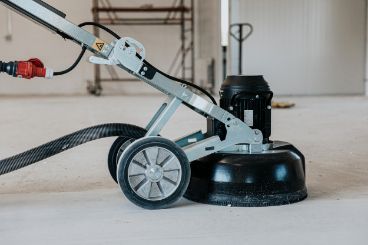
Dry method
A dry method of concrete floor polishing uses a compound that sinks into the concrete, protecting it from the inside out. A good finish requires no further polishing, and this method is excellent for new floors. However, before applying this type of sealer, you must ensure that your concrete floor has been cured for seven days with water. This will ensure your floor is fully protected, and you won't need to worry about maintaining it. You can also use a commercial polishing compound to clean up any surface residue.
Concrete polishing is a cost-effective and efficient way to improve the look of your floor and make it stronger. The result is a smooth and shiny floor with the same look as marble and granite. The dry method of concrete floor polishing uses large commercial-scale polishing machines and different abrasive polishing disks. These disks come in varying textures, from coarse to fine.
When choosing a concrete floor polishing method, ask your contractor which method they prefer. The dry method is often the most popular option today. It requires less water than the wet method but produces less dust. A dry polish will give your floor a high shine without a large amount of dust, which makes it ideal for food and beverage facilities. However, waiting until your concrete has sufficiently hardened would be best before choosing a dry method.
If your concrete floor is good enough to handle this polishing, you can start with a diamond grit before moving on to a more advanced level. This can take two passes depending on the density of the concrete floor. For extra protection, consider applying a liquid chemical hardener to your floor before the polishing process. This will help solidify the concrete and reduce staining and water penetration. In addition, a hardened floor produces a higher polish.
Dry method of concrete floor polishing benefits homeowners by reducing cleaning and maintenance costs. This type of floor is more durable and reflects light better than its wet counterpart. It is also more aesthetically appealing and offers a more sophisticated look. Additionally, it is more energy efficient.
Level of sheen
A few factors determine the sheen level of your polished concrete. A high sheen level means the floor reflects light well, which can increase safety and improve the image of your space. A lower sheen level means that the concrete has an uneven appearance. Also, the shine you achieve will depend on how much aggregate you want to expose.
Level four is the highest sheen level. This finish will allow you to see the reflection of light from all angles and may even look wet. Typically, level four polishing is performed using resin bond diamond. In some cases, a high-speed burnisher may also be used.
When it comes to concrete floor polishing, there are several different options available. The first level is ground polish. This will leave the floor with a matte finish with little reflection. The second level is called honed. This will leave the floor with a low-sheen finish that has some overhead reflection.
Concrete polishing is a professional procedure that requires extensive equipment and training. It is recommended that you hire a professional for the process. A qualified technician can polish the surface and increase its sheen, making it more stain-resistant and slip-resistant. A skilled technician will also know how to repair any damage caused by the process.
Regular maintenance is necessary to preserve the shine of polished concrete floors. It is important to remember that regular wear, weathering, and foot traffic can reduce the sheen of a floor. Using the wrong cleaning products can also decrease the sheen. A professional will use a chemical product to clean the floor properly.
The level of sheen you achieve depends on many factors, including the amount of aggregate that is exposed. Different types of concrete polishing will leave varying degrees of aggregate exposed. For example, if your concrete floor is in a manufacturing space, you may not want to expose all the aggregates.
Repairing minor floor imperfections before polishing
Before beginning the concrete floor polishing process, it's important to address minor floor imperfections. These imperfections may require minor repairs, such as rebuilding joints, addressing craze cracking, or filling pits and voids. Some minor flaws may also require colour matching using dyes. In any case, the condition of the floor will have the most impact on the final results. This condition will determine what type of diamond tooling is required, how long the floor needs to be polished, and how many grits to apply.
The appearance of a polished floor is essential, but dirty floors can also be detrimental to a business. A dirty floor not only decreases employee morale but can also increase health risks. Clean, durable floors streamline operations and reduce costly repairs while enhancing the interior atmosphere. Polished floors are also easier to maintain than non-polished ones, increasing light reflectivity and improving customer satisfaction.
Even though polished concrete looks good, it can be prone to damage over time. This can be caused by exposure to harsh cleaning solutions, impact, and high foot traffic. Another common cause is a poorly laid foundation. This causes air pockets and bubbles, which can eventually lead to cracks. By repairing minor imperfections before polishing, you'll be able to preserve the lustre and shine of your floor for years to come.
Before concrete floor polishing, you should fix any minor floor imperfections. For instance, a floor with multiple cracks may need to be repaired before concrete floor polishing. Large cracks, meanwhile, can require additional steps. Expert floor specialists may use a diamond blade to widen them and an adhesive material to attach to the sides of the slab.
Some minor floor imperfections that may require repair before polishing are craze cracks, hairline cracks, and carpet tack strips. For small divots and spalls, you can use a cement-based patching compound. Also, if your concrete floor has cracks, check for moving cracks. Active cracks are the type that moves.
Contact us today at 08 9567 0487 if you are ready to take your concrete floor to the next level! We can help you achieve your dream flooring!
FREE INSTANT QUOTE!
**plus FREE bonus coupon**
Contact Us
You might also like
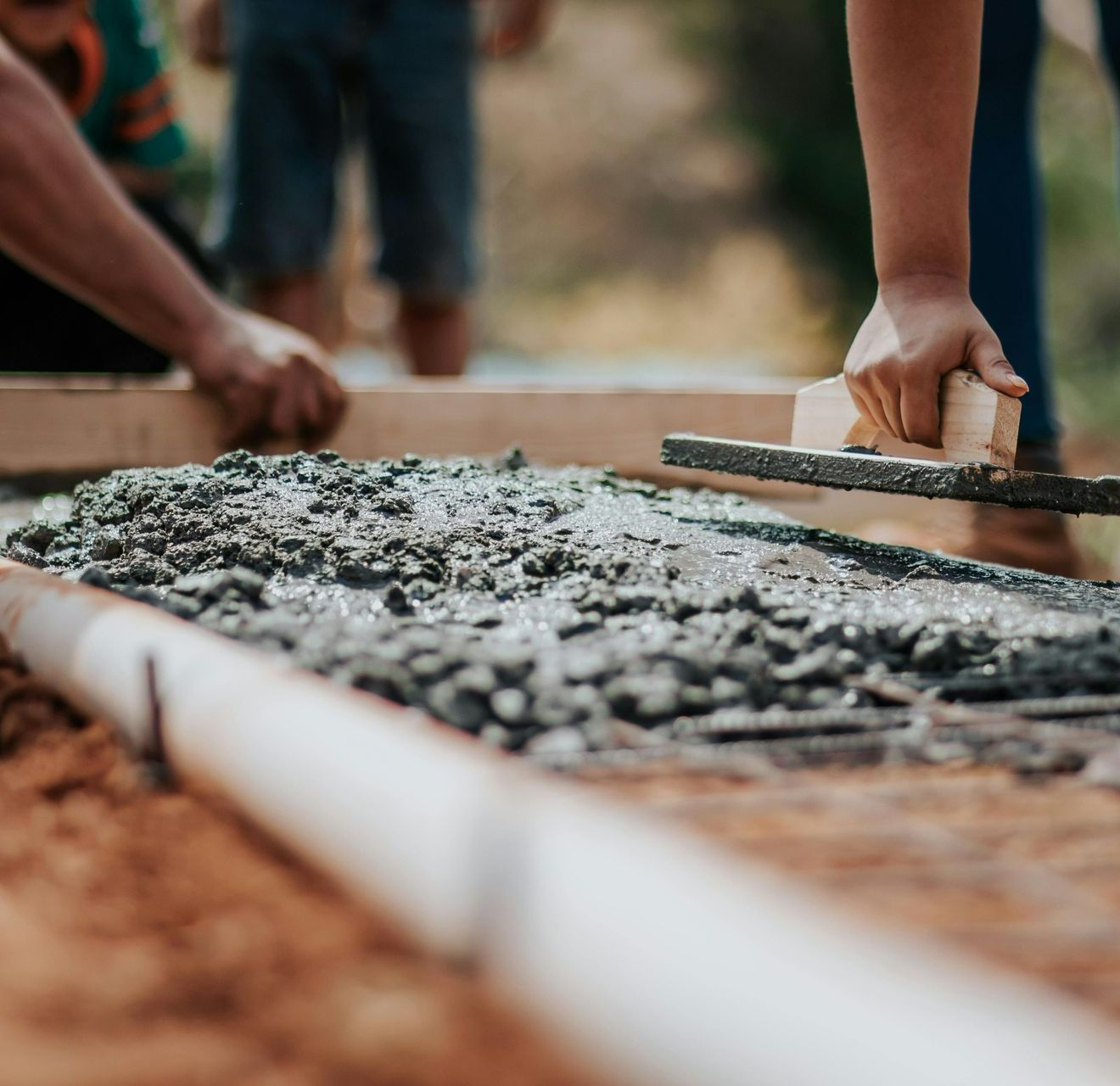
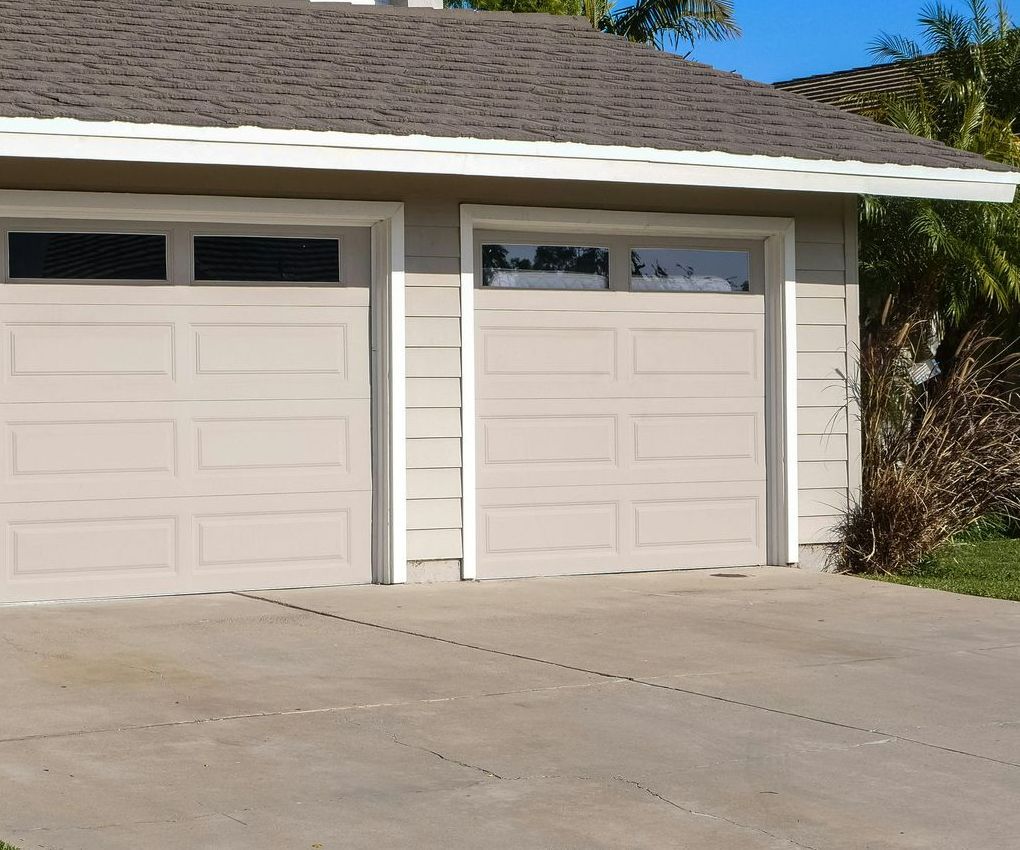
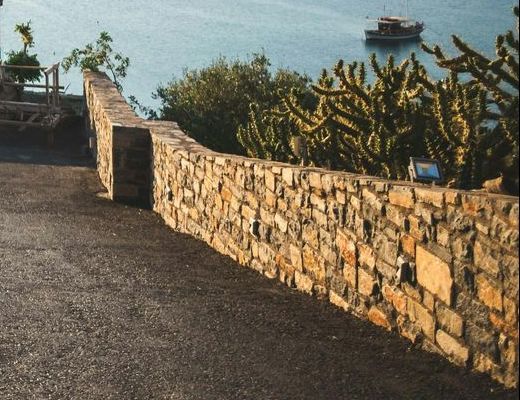